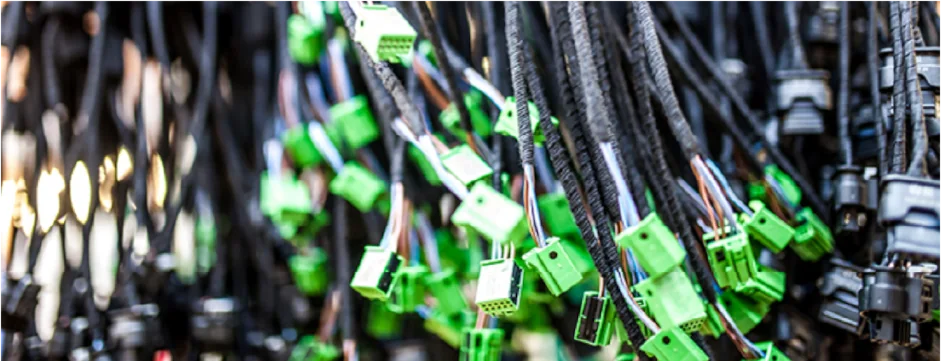
We are specialists in cable harnesses, both in their production and in supporting their development. We manufacture and supply solutions for a variety of industries from automotive, white goods to special machinery piece production.
Our cable harnesses can range from a few centimetres to ten metres and we are one of the few companies to produce flat FFC cables (Flexible Flat Cables) and assemblies using them. We are also able to create complex solutions from cable harnesses connected to PCBAs and other components.
We offer the following types of work:
- cutting
- stripping
- tinning
- crimping, splicing
- soldering
- binding
- connectors assembly
- crimping of terminals
- cable bonding (with water protection)
- compacting – resistance welding
- sealing
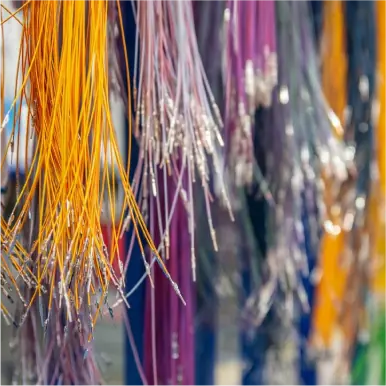
How do we produce?
Quality cable harnesses are needed not only for every car. In our company we have been manufacturing and assembling cable harnesses of various types and complexities for more than 15 years. Quality control.
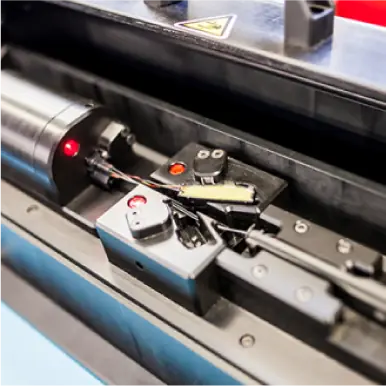
Quality control
Before the finished cable assembly reaches our customers, it undergoes a series of stringent parameter and quality checks so that we can always guarantee that you are getting the best possible product.
We do so, among other things:
- electrical tests
- mechanical tests
- pressure tests
- water tests
- tear tests
- metallographic cut
- 2D and 3D measurements
- X-ray
Connectors from following suppliers are used
Aptiv
Molex
Stocko
Hirschmann
JAE
TE Connectivity
Yazaki
Sumitomo
Lumberg
JST
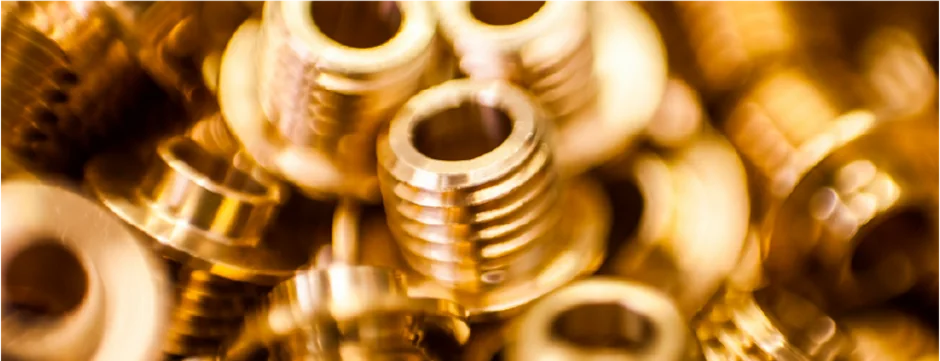
Our production on CNC machines has a thirty-year tradition and thanks to our focus on the highest quality and automotive cleanliness we can offer even very complex workpieces with superior precision. We process all types of steel, brass and duralumin and can design the most efficient production process including the provision of appropriate tooling.
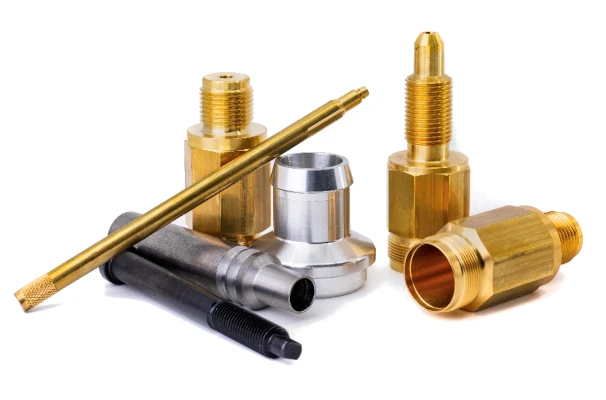
How do we produce?
Modern computer-controlled machining is the most accurate and fastest machining method available today. Therefore, the machine park of Hronovský s.r.o. includes a total of ten STAR CNC machines (SR20, SR32, SB12), which allow us to efficiently process both smaller and larger orders.
- we machine all kinds of materials (steel, brass, stainless steel, duralumin...)
- we process batches starting from 500 pieces
- we can arrange all surface treatments for you (including chrome plating and gilding)
- machining of bar materials up to Ø 36 mm
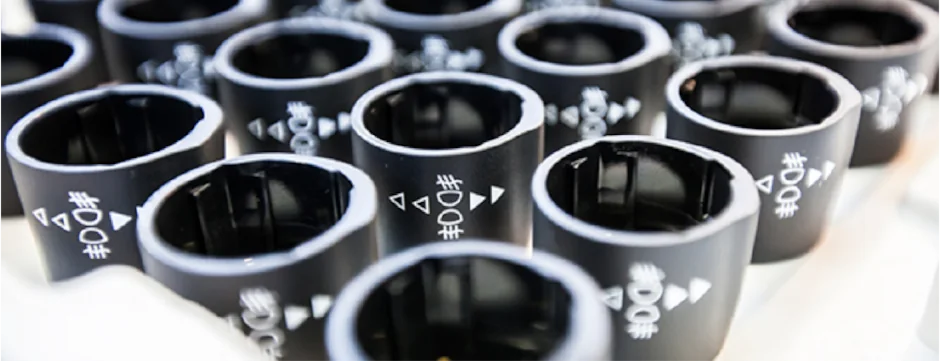
We are specialists in all aspects of plastic and metal moulding and can solve even the most complex requirements, whether they concern the moulding of clean plastic parts, the plastic overmoulding of metal parts, or the stamping out of contacts from band. We can make and service moulds, add automation to presses and much more. We have more than sixty presses of different types and sizes up to 700 tons of clamping force and our specialty is not only overmoulding but also 2K products, i.e. parts made of two different materials including elastomers.
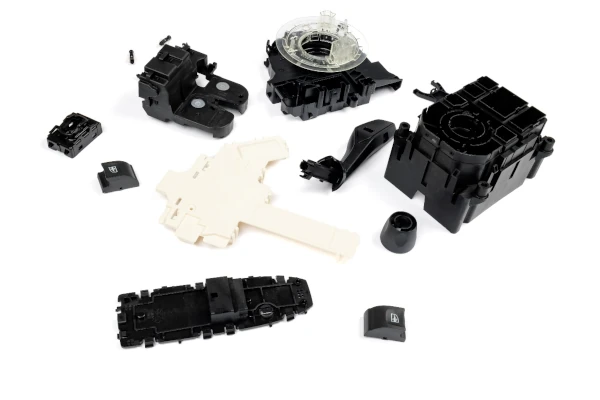
How do we produce?
Whether you are interested in moulding clean plastic parts, plastic overmoulding of metal parts or stamping out contacts from strip metal, our company is here for you. We have over fifty professional presses of various types that can meet a wide range of your requirements, such as:
- 62 injection moulding machines with clamping forces from 25 tonnes to 700 tonnes
- moulding of clean plastic parts
- 14 spraying or carousel presses with rotary and sliding table with clamping force from 25 to 150 tons
- injection of stainless steel socket contacts into electronic units
- plastic overmoulding followed by cutting
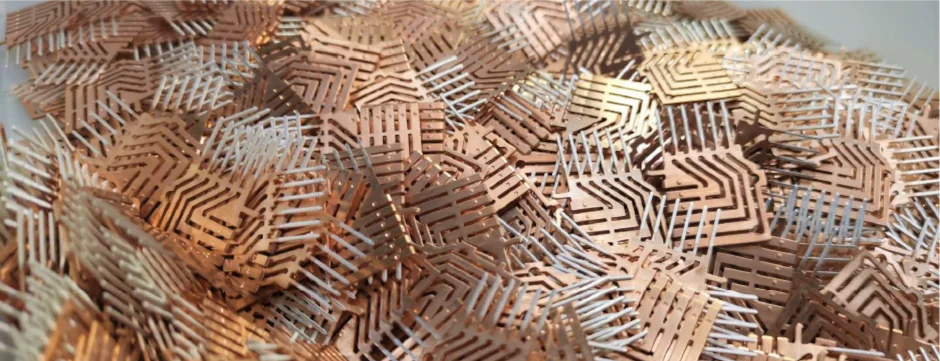
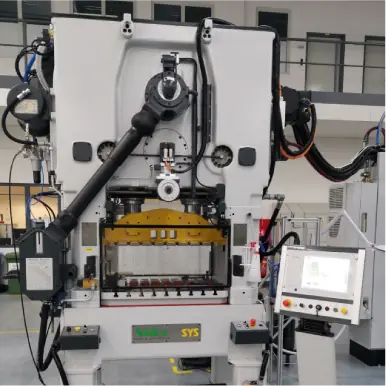
How do we produce?
The metal pressing plant is equipped with Bruderer presses with a shearing force of 500kN and a speed of up to 1120 strokes per minute. These Bruderer BSTA50EL high-speed presses are synonymous with precision, performance and reliability. They are designed for series production of stamped parts, electro-contacts, etc.
We use various types of metal strip as input material and all casting work is carried out on shearing and forming tools. Last but not least, we inspect our parts using a Micro-Vu Vertex 310 optical measuring machine. We also provide electroplating for our customers according to their requirements.
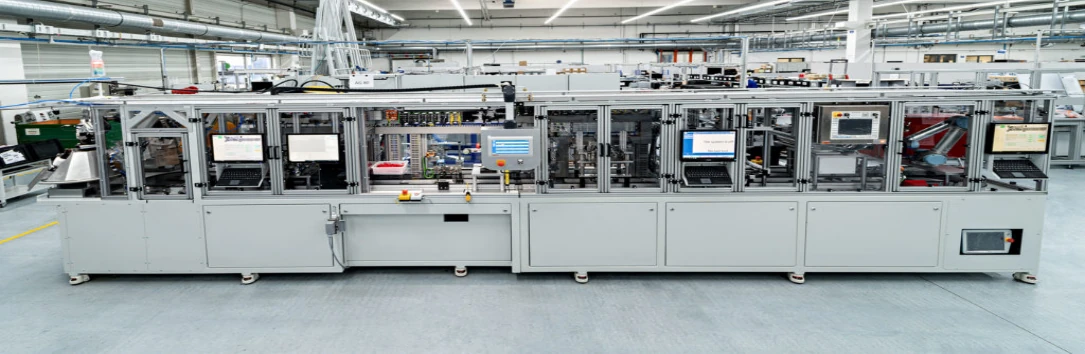
Automation
Comprehensive services including design, construction, manufacturing, installation and training in the field of automation and robotics.
Inquiry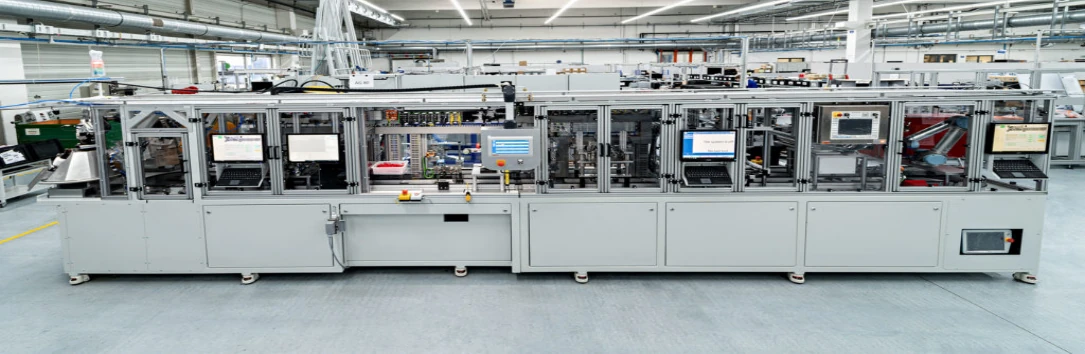
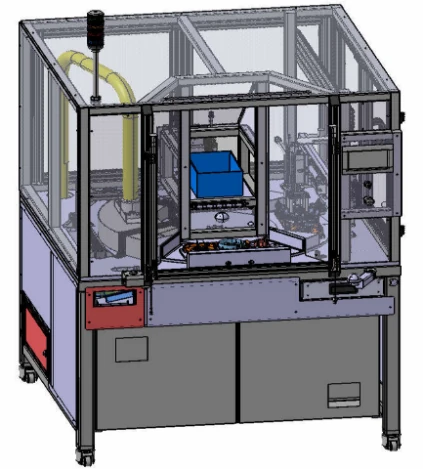
What are we doing?
We build test and inspection stations, jigs, assembly stations, automatic production lines, EOL testers, etc. for our customers. We offer turn-key project solutions from A-Z, including commissioning, warranty and service.
Are you interested in knowing more?
More information about the HRO-TECH company can be found at www.hro-tech.cz
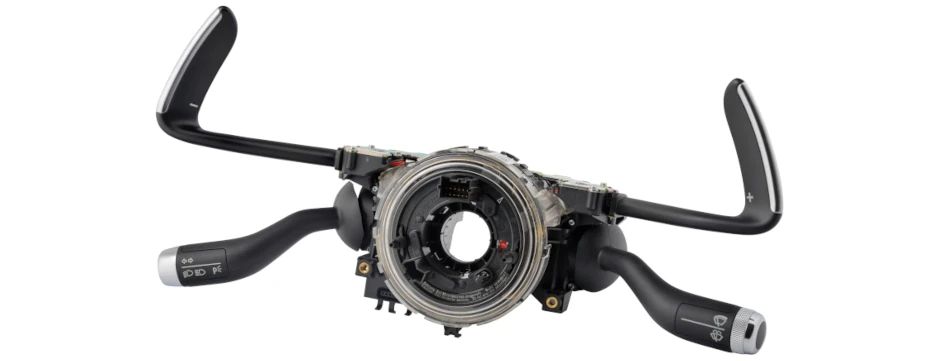
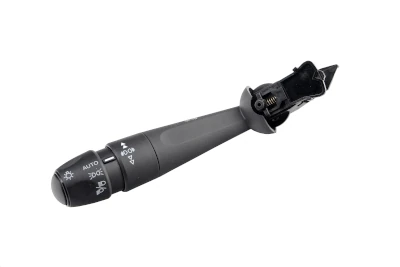
How do we produce?
We manufacture high-quality mechatronic components, especially steering wheel levers, for most European cars. They are supplied all around Europe from our plants in Náchod and Smolyan, and before they reach the customers they undergo a series of strict parameter and quality checks so that we can always guarantee that you are getting the best possible product.
These are:
- Electric tests
- Mechanical tests
- Pressure tests
- Waterproof tests
- Pull off tests
- Metallographic cut
- 2D a 3D measurement
- X-Ray tests
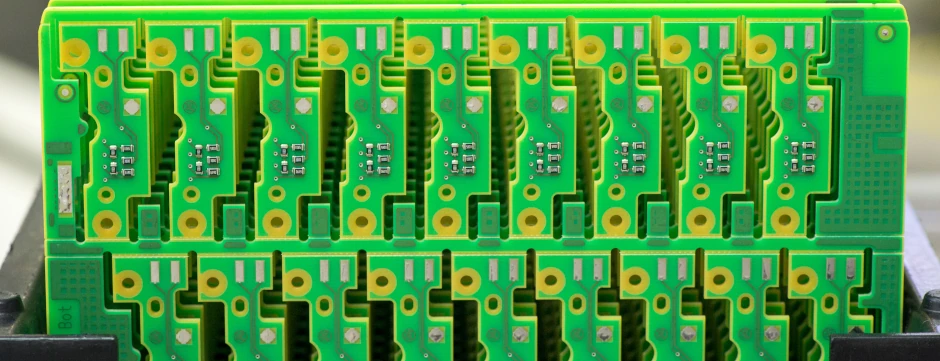
SMT (Surface Mount Technology) plays a key role in the creation of most of the devices that power our world, and we at Hronovský s.r.o. are extremely proud to be one of the European leaders in this type of manufacturing. We use the most advanced techniques and equipment to ensure the highest quality and efficiency in every step of our manufacturing process with IATF 16949 and VDA 6 standards, which are the applicable quality access control system in the automotive industry.
With years of experience and expertise, our team of dedicated professionals carefully organise every stage of SMT production to turn even your most creative concepts into reality. Our state-of-the-art equipment not only handles even complex designs with ease, but also ensures noticeably shorter lead times without compromising on quality. Whether you want to produce complex printed circuit boards for consumer electronics or robust components for industrial applications, our adaptable production processes are at your service.
We currently use or perform: laser, SPI, SMT, AOI, ICT/FCT, milling, wave soldering and final inspection processes. In addition, 3 SMT lines with Juki super-fast modular milling machines and Depanelling DIVISIO 500 series - an intelligent system that interprets the status itself and also controls maintenance and optimization processes as needed. This allows us to produce up to 150,000 more parts per year.